Finished reading?
Tell us what you think!
Copyright © BASF SE 2018
“We planned to do everything we could to stay running without compromising safety.”
— Matthew Auger
Operations Director
As Port Arthur employees hunkered down in conference rooms between shifts, a poker game played with sugar packets helped lighten the mood in the tense days following Hurricane Harvey. White packets were a dollar, blues were $5, yellows were $10 and pinks were $15.
“This was later in the week, when we started to get into a routine,” recalls Operations Director Matthew Auger. He helped lead the 60-person Hurricane Response Team that kept the site running 24-7 during and after the storm. They worked and slept in shifts on cots set up in offices and conference rooms.
BASF’s Port Arthur site is home to one of the world’s largest steam crackers, which transforms crude oil and natural gas into chemical building blocks. The facility produces roughly 20 million pounds of product in a single day. Aside from impacting customers, shutting down a site as large and complex as Port Arthur is immensely difficult and can cause environmental emissions, equipment damage and other hazards.
From the moment they were activated, the team had a singular goal. Auger explains: “We planned to do everything we could to stay running without compromising safety.”
So for an entire week beginning Monday, August 28 – the day before flash floods started in Port Arthur and nearby Beaumont – Auger and his colleagues stayed put and stayed focused. As their homes took on water, as spouses and kids relocated to hotel rooms or the homes of friends and family members, the team held that goal in sight.
The hurdles kept coming. It wasn’t luck on their side, but years of training and essential preparation that got them through each one, according to Site Manager Greg Masica. “The team performed at their peak amidst the storm. But they wouldn’t have been able to do what they did if their colleagues hadn’t done the right thing well before the storm hit,” says Masica.
Just twelve months prior, the Port Arthur team had diagnosed a vulnerability in its steam-generating systems. They realized that if an instrument panel was compromised, the boilers would shut down, so they had the system reconfigured. When Harvey’s deluge caused the instrument panel to trip, they were ready.
“Extraordinary” is how Masica describes the feeling of seeing that preparation pay off. “In some cases we knew, ‘We have six hours to fix this. If we don’t fix it, all the other challenges that are two, three, four days away don’t matter.’” Asked if he’s proud of their success, Auger clarifies: “We didn’t cowboy it. We’re proud, but we were always ready to shut down if needed. We also knew the serious impact a shutdown would have and wanted to avoid it if reasonably possible.”
At the height of the flooding that evening, colleagues stayed in touch with their loved ones but were unable to leave the site as the situation worsened outside. “It started becoming very real for people,” Auger remembers. “We rounded everyone up and assured them that as soon as things cleared up in the morning, we would do everything we could to help their families.”
This is the challenge of keeping a site running in extreme conditions: even the most bulletproof hurricane plan needs an excellent, focused team to execute it. If designing the perfect plan is a science, keeping teams housed, fed and cared for is an art that requires compassion and a willingness to do whatever it takes.
That compassion came through in the form of financial help, supplies and temporary housing that was provided to employees and their families, says Auger. “Opportunities like that only come so many times in a career, and BASF has made some lifelong employees by the way the company responded. It was tremendously appreciated.”
Like so many others who depended on the kindness of colleagues, Auger spent his first free night at the home of a coworker who had taken in his wife and daughter when they lost power and water. “I got to watch college football and saw my daughter and my wife for the first time in a week,” he says. “That was nice.”
“I was extremely proud of them. People were taking care of things that needed to be taken care of in the midst of their own personal crisis.”
— Greg Masica
Site Manager
A less competent team might have disintegrated under the constant pressure. “To me that’s an indicator of the true capabilities, skills and talents of our team,” Masica says. “I was extremely proud of them. People were taking care of things that needed to be taken care of in the midst of their own personal crisis.”
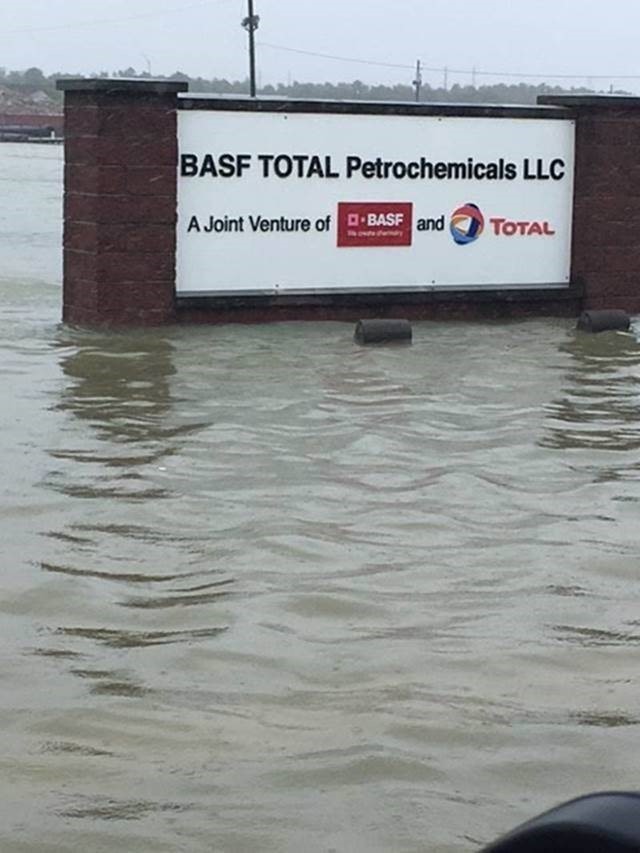
Anatomy of a shutdown
Conducting a maintenance shutdown takes weeks or even months of planning. Time is a luxury teams don’t have when bad weather is on its way. This example timeline shows how employees work around the clock to shut down operations and bring them back online after a weather event.
*Days consist of two 12-hour shifts
How Port Arthur faced the storm and kept on going.
BY LAURA ENDERLE
Running against the odds
